March
2024
Behind the Scenes of Production: Unveiling the Secrets of Rubber Compounds with BOGUMA s.r.o.
From rubber flooring tiles to electrical insulating blankets, each of our products is unique in its composition. Thanks to the expertise of the team of professionals at BOGUMA s.r.o. we know how to use various rubbers and rubber compounds for the benefit of our clients. How? Read on to find out.
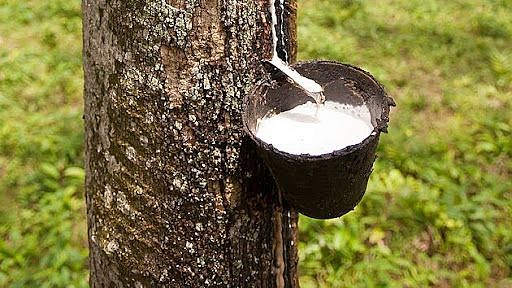
Welcome to the fascinating world of rubber compounds, where innovation and precision meet the demands of modern industrial sectors. At BOGUMA s.r.o., our commitment to quality and excellence leads us to continually explore and utilize a wide range of rubber compounds to meet the diverse needs of our customers. Join us on a journey through the world of rubber, where we not only delve into the intricacies of the rubber industry but also learn more about our manufacturing processes and the expertise of our director, Teodor Puhu, who generously shares his unmatched knowledge of rubber.
Not All Rubber is Created Equal
Rubber compounds play a crucial role in various industries, from automotive to construction, offering unique properties tailored to specific applications. At BOGUMA s.r.o., we carefully select and utilize various types of rubber compounds to ensure the optimal performance and durability of our products. The fundamental division of rubber compounds includes:
- natural rubber
- synthetic rubber derived from a combination of synthetic compound
Natural Rubber (NR):
Derived originally from latex, protein-rich milk is produced by certain plants, particularly the Hevea brasiliensis tree (Brazilian rubber tree). Natural rubber has been known in Europe since roughly the mid-18th century. Rubber trees for its production were cultivated until the second half of the 19th century only in South America, later also in Southeast Asia (Vietnam, Indonesia, and Malaysia).
Derived from latex, natural rubber offers unique properties such as high elasticity and resilience, making it suitable for various applications. At BOGUMA s.r.o., we often combine natural rubber with other synthetic rubbers and additives to enhance specific properties such as abrasion resistance or tear strength. Among our products, you will find pure natural rubber in the form of para rubber.
Rubber compounds containing natural rubbers contribute to the resilience and reliability of our products and are used, for example, in conveyor belts.
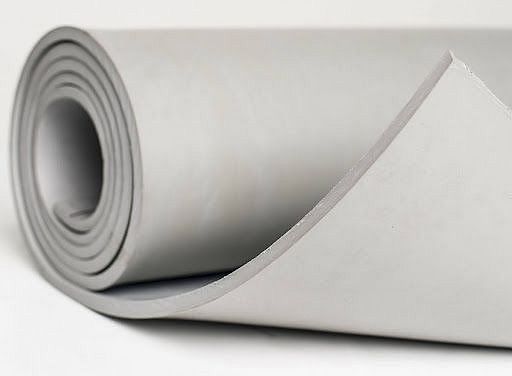
An example of our Para rubber 7689
We use:
- NR, SVR 3L, SVR 10
- Mooney viscosity ML (1+4) 100°C
Natural rubber in our products:
Rubber Compounds Mixed Using Synthetic Rubbers
The goal of the rubber industry is constant improvement. It is therefore not surprising that synthetic rubbers gradually began to be added to natural rubbers to complement and enhance their properties. Unlike natural rubber, synthetic rubbers are created artificially, mainly from petroleum and various special chemical additives using polymerization. The precision of synthetic production allows for specific product properties depending on the ingredients and processes used, such as oil resistance, high-temperature resistance, abrasion resistance, and more.
Some of the most important examples of rubber compounds made from synthetic rubbers include:
- BR (Butadiene Rubber)
- SBR (Styrene-Butadiene Rubber)
- NBR (Nitrile Butadiene Rubber)
- EPDM (Ethylene Propylene Diene Monomer Rubber)
- CR (Polychloroprene Rubber)
1. Cis-1,4-Polybutadiene (BR):
Butadiene rubber or BR was first synthesized in the laboratories of German chemists in the 1920s. Initially developed as an alternative to natural rubber, which was limited in availability and subject to occasional price fluctuations. BR began to gain popularity in the interwar period as it allowed for the production of cheaper and more reliable tires, contributing to the growth of the automotive industry.

An example of BR being used in our product Rubber sheeting 7750 NR-SBR-BR
It excels in exceptional abrasion resistance, making it an integral part of our production of abrasion-resistant rubber products. BR rubber compounds excel in applications where abrasion resistance is important, such as conveyor belts and industrial seals. With their high resistance to wear and tear, BR rubber ensures long-term reliability and performance in demanding environments.
We use:
cis-1,4-polybutadiene with 96% cis structure
enhances oil resistance
Mooney viscosity ML (1+4) 100°C
BR rubber compounds in our products:
2. Nitrile Butadiene Rubber (NBR):
Nitrile Butadiene Rubber, or NBR, is valued for its excellent oil resistance, making it an ideal choice for applications exposed to various oils and fluids. At BOGUMA s.r.o., we incorporate various grades of NBR rubber compounds into our products to ensure flexibility and resilience in environments where exposure to oils is common. It is also resistant to many chemicals, making it suitable for environments with frequent chemical exposure.
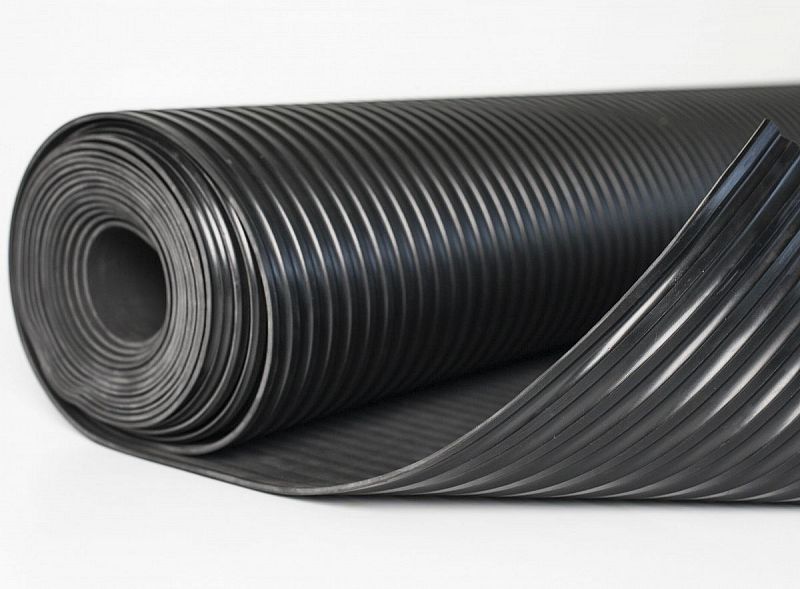
An example of NBR being used in our product Black flooring oil resistant wide ribbed S1 NBR45
Its uses vary depending on the final form of the product. It is used, for example, in the production of various industrial components such as hoses, seals, rubber parts, and others that come into contact with oils or chemicals.
We use:
butadiene-acrylonitrile copolymer with 33% ACN content
Mooney viscosity ML (1+4) 100°C
NBR rubber compounds in our products:
3. Styrene Butadiene Rubber (SBR):
Styrene-butadiene rubber, or SBR, is a synthetic rubber derived from styrene and butadiene. It was developed as a replacement for natural rubber during the Second World War when natural rubber supplies were cut off. Since then, SBR has become a staple in the rubber industry, valued for its excellent abrasion resistance, durability, and versatility.
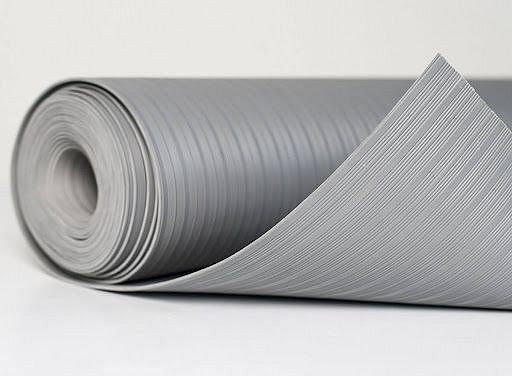
An example of SBR in our product Coloured flooring basic fine ribbed S2-SBR
It is commonly used in the production of tires, conveyor belts, and various molded rubber goods. In combination with other rubber compounds, SBR enhances properties such as abrasion resistance, tear strength, and flexibility, making it an essential component of many rubber formulations.
We use:
styrene-butadiene rubber with 23.5% styrene content
Mooney viscosity ML (1+4) 100°C
SBR rubber compounds in our products:
4. Ethylene Propylene Diene Monomer Rubber (EPDM):
Ethylene-propylene rubber, or EPDM, was first produced in the early 1960s. In the mid-1960s, EPDM membranes for waterproofing were manufactured from a mixture containing EPDM, rubber fillers, oil, additives, and vulcanization agents. The first roof of a restaurant at Chicago airport was realized in 1967. A significant development in the production and application of EPDM waterproofing materials occurred in the 1980s.
Since then, EPDM has been sought after for its exceptional resistance to weathering, making it an ideal choice for external applications. At BOGUMA s.r.o., we utilize EPDM rubber compounds in products requiring resistance to weathering, acids, ozone, and UV radiation. From automotive seals to roofing membranes and the food industry, EPDM rubber compounds provide long-lasting durability and performance even in demanding environmental conditions.
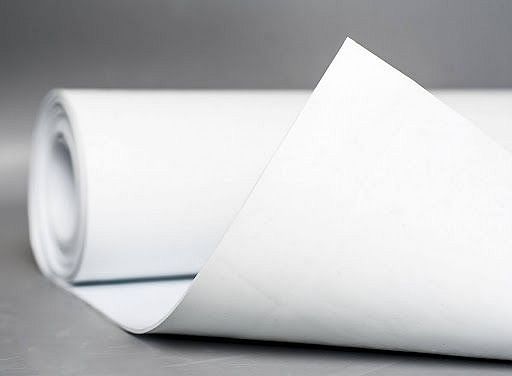
An example of EPDM in our product White rubber sheeting food grade TD 7816-EPDM-NR
Since then, EPDM has been widely used for its excellent resistance to heat, weather, and ozone. It is valued for its outstanding durability and resistance to aging, making it suitable for outdoor applications where exposure to sunlight and weathering is common.
EPDM rubber is commonly used in the automotive industry for weather sealing, in construction for roofing membranes, and in various industrial applications. At BOGUMA s.r.o., we incorporate EPDM rubber compounds into our products to ensure long-term reliability and performance in demanding environments.
We use:
terpolymer of ethylene, propylene, and a diene monomer
Mooney viscosity ML (1+4) 125°C
EPDM rubber compounds in our products:
EIP 0 electrical insulating blanket
5. Polychloroprene Rubber (CR):
Chloroprene rubber, or CR, was developed in the 1930s and became popular for its excellent properties and wide range of applications. It is a synthetic rubber known for its excellent resistance to weather, ozone, and oil. It is commonly used in applications requiring resistance to harsh environmental conditions, such as automotive seals, gaskets, and more.
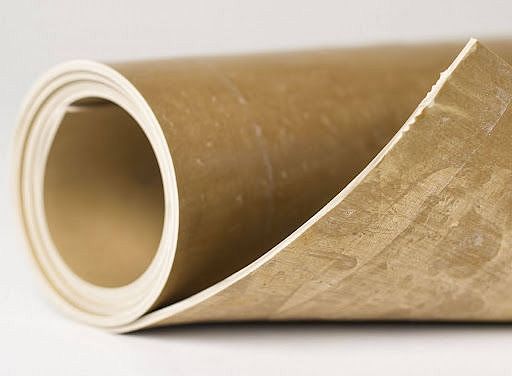
An example of CR in our product Rubber sheeting soundproof TD 9001 — CR-NR
CR rubber offers good mechanical properties, flexibility, and resilience, making it suitable for various demanding applications. At BOGUMA s.r.o., we incorporate CR rubber compounds into our products to ensure long-term reliability and performance in challenging environments.
We use:
polychloroprene rubber with 70% chloroprene content
Mooney viscosity ML (1+4) 100°C
CR rubber compounds in our products:
Excellence and Expertise in Manufacturing
Behind every exceptional product stands a team of dedicated professionals, and at BOGUMA s.r.o., our director, Teodor Puha, embodies a spirit of expertise and dedication. With a career that began decades ago in the rubber industry, Teodor brings invaluable experience and knowledge to our operations.
His journey began in 1978 at the age of 15 when he decided to study and advance in the rubber industry. Over the years, he honed his skills, gradually transitioning from manufacturing positions to leadership roles. Since joining BOGUMA s.r.o. in 2005, Mr. Puha has helped our company grow with his unparalleled expertise and extensive knowledge of rubber compounds.
Innovation and Loyalty
Innovation lies at the heart of everything we do at BOGUMA s.r.o. We constantly strive to adapt to the changing dynamics of the industry and customer requirements while maintaining the highest standards of quality and reliability. Our collaboration with reputable suppliers of rubber compounds and our commitment to rigorous testing ensure that every product meets our strict performance and durability criteria.
Since 2007, we have been cooperating with the Czech company Gumotex, with whom we are extremely satisfied. They are our primary supplier of colored rubber compounds. Another Czech company, Rubena, with whom we established contact in 2008, assists us mainly in the production of black rubber compounds. For 10 years now, we have also trusted Gumárny Zubri, who have been in the market for 85 years. We work with multiple suppliers primarily for safety reasons, ensuring that we can always guarantee our clients' timely production and delivery of the product, as the rubber industry is often unpredictable, and unfortunately, we never know when there may be a shortage of raw materials or an unexpected production outage.
"Similarly to a three-legged chair with uneven legs ensuring stability on uneven surfaces, our trio of suppliers guarantees stability for us in the rubber industry."
- Teodor Puha, director at BOGUMA s.r.o.

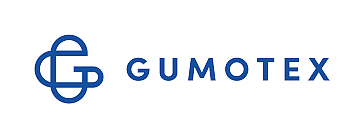
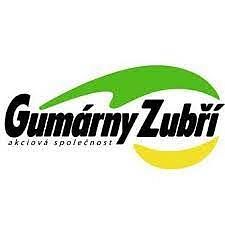
Development of New Rubber Compounds
Regarding the development of new rubber compounds for our products, it is a complex and time-consuming process governed by certification requirements and modifications to existing products. For example, changing the thickness of a product can be relatively quick, taking approximately 6-8 weeks, with the physical-mechanical properties remaining unchanged and only the visual character being altered. When developing entirely new products, however, we operate on a longer time horizon, with laboratory testing and large-scale testing being important parts of the process.
At the beginning of development, the availability of raw materials from our suppliers is assessed, and additional quantities are procured if needed for testing. The formulation is repeatedly adjusted and tested to ensure that our products always meet the desired parameters and comply with current regulations and standards. Products go through multiple testing phases, resulting in continuous improvement of products that never stagnate.
For example, the development cycle of our electrical insulating blanket required a lengthy process, lasting two and a half years. We are proud that despite the limitations of laboratory capabilities, we successfully managed testing. In the initial stages of development, we encountered failures in laboratory tests as our production equipment could not process the given compounds. As a result, we had to adjust the formulations four or five times to achieve the desired result. This example illustrates our ability to adapt and our determination in developing new products, even under challenging conditions.
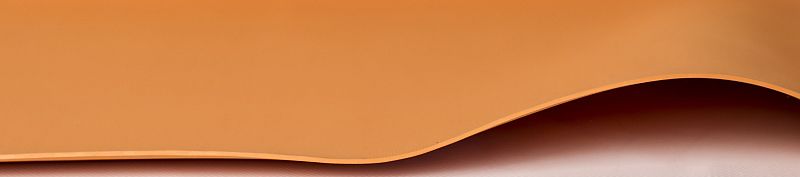
Our Electrical Insulating Blanket
At BOGUMA s.r.o., we are committed to excellence in rubber technology, delivering high-quality rubber compounds that meet the most demanding requirements of our customers. With our state-of-the-art facilities, advanced technology, and experienced team of professionals, we offer innovative products and solutions that drive performance, reliability, and sustainability across various industries.
Contact us today at info@boguma.sk to learn more about our products and services and discover how we can help you achieve your goals. Visit our Usage subpage to discover all the practical usages of our products.
Do you wanna chat with us online? Leave a comment under our LinkedIn post and get the discussion going!
Let BOGUMA s.r.o. be your trusted partner for all your rubber compound needs. Together, we can shape the future of the rubber industry and drive innovation and excellence for years to come.